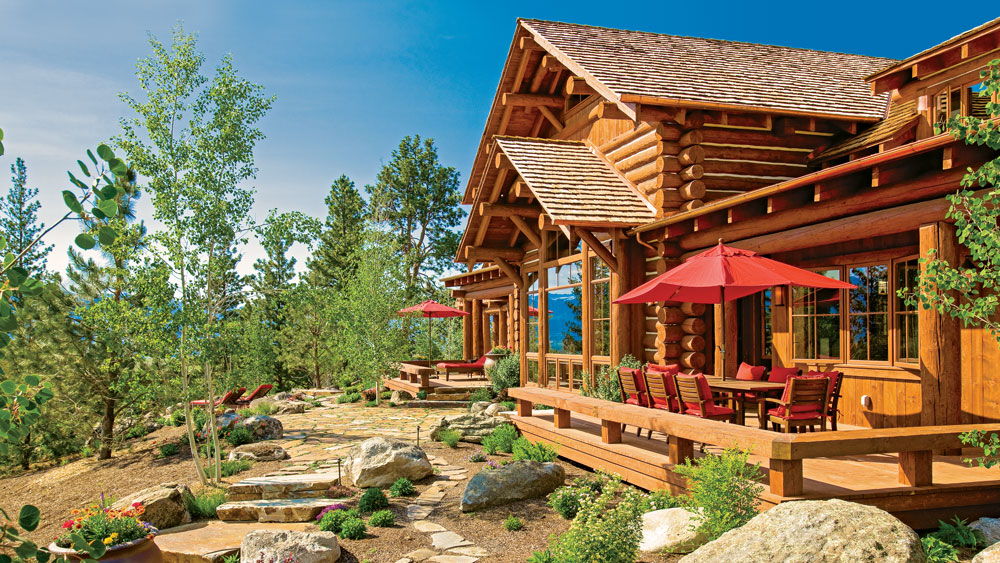
Dozens of species of wood are commonly used to build log homes in North America. Almost all are softwoods: evergreens such as pine, cedar, fir, cypress and spruce, though some hardwoods, like oak, are also used. Though each log home producer favors certain species, the successful use of so many varieties is a clear indication that thereâs not one type of tree that makes a better log home than another. Instead, the choice rests in the type of wood your log home company and you prefer. Despite their differences, these various woods share certain characteristics.
Wood Science
Technically, wood is the hard, fibrous substance beneath the bark of a tree. It owes its character to the hollow, spindle-shaped cells that constitute it. These cells are arranged parallel to each other along the tree trunk, and this arrangement affects some properties of the wood, notably strength and shrinkage. The woodâs fibrous nature influences how it is used.
Trees grow by adding new wood. Wood that has already been formed does not continue to grow, but each year, a new layer of wood, called an annual growth ring, is added. The portion of the ring formed in the spring is light in color and is called earlywood. The portion formed later in the growing season is darker and is called latewood. Latewood is generally denser and stronger than earlywood.
The wood formed just inside the bark is known as sapwood. Depending on the size and species of the tree, sapwood can measure 1 to 3 inches beneath the bark. As a rule, the more vigorously growing tree species have wider sapwood layers. Second-growth trees of marketable size consist mainly of sapwood.
See also How to Heat and Cool Your Log Home Efficiently
Sapwood contains mostly living cells that carry sap, the treeâs food, from the roots to the leaves. Itâs not durable, and if exposed to moisture and other factors, it can decay. But in terms of log home construction, sapwood usually absorbs preservatives readily, so when wood is treated with a quality preservative, the presence of sapwood can be an advantage.
Inside the sapwood is the heartwood. Heartwood consists of inactive wood cells that have been changed slightly, both chemically and physically, so that they no longer conduct sap. Heartwood is usually more decay resistant than sapwood.
Wood Traits
Wood has several distinguishing qualities that affect its use for log home construction. Grain usually refers to the logâs annual growth rings or to the arrangement of the wood fibers. Annual rings are said to have either a fine or a coarse grain. Fine-grained wood, such as ponderosa pine, has narrow, inconspicuous annual growth rings and closely spaced pores. In contrast, coarse-grained wood, such as southern yellow pine, has wide, conspicuous annual growth rings.
Texture, used synonymously with grain, usually refers to the size, appearance and quality of fibers in the wood. The earlywood in coarse-grained wood is light in color and soft in texture. Latewood is typically darker and harder.
The arrangement of a logâs fibers, referred to as either straight or spiral grain, can affect a logâs structural properties. Some arrangements are considered more desirable for building than others. A straight grain, where the fibers run parallel to the length of the wood, can be highly desirable. This wood tends to remain straight while it is drying. A spiral grain, where fibers swirl around the tree trunk, is less desirable because cut timber tends to twist as it dries. Woodâs strength derives from its cellular makeup. Its cells (hollow, cellulose blocks) are bonded by a substance called lignin. The resulting material is stronger, pound for pound, than steel. Lignin also tends to be an elastic material that adds to woodâs resiliency.
See also Your Log Home Foundations
For some wood used in log homes â such as rafters, beams and posts â strength, resiliency, hardness and shock resistance are important considerations. But for logs stacked in the walls, strength and resiliency arenât as critical, as one single log wonât carry the load alone. Log home producers refer to engineering calculations to determine the proper size or species of wood for each job.
Woodâs weight varies greatly from the time itâs first cut and saturated with water until it is dry. Woodâs weight is an important consideration in determining the mass of individual logs as theyâre lifted into position, and, more importantly, the load of the entire house as it rests on its foundation.
Insulating Properties
Wood has several thermal properties that affect its energy efficiency.
In the simplest, most easy-to-understand terms, wood reacts to heat retention and release in much the same way as stone. Take a good sized rock and set it outside in the summer sun all day. Then as dusk falls and temperatures cool, bring it inside. Depending on its size, that stone will continue to emit the heat it absorbed for hours. Logs work the same way. This is thermal mass in action.
Thermal resistance is the insulating value of a material. This resistance to heat flow, usually expressed as R-value, varies among wood species and depends on the woodâs density and other qualities. While R-values alone arenât a proper measure of the energy efficiency of a log wall, they are widely used. This is why looking at the full picture of a logâs thermal properties â not simply judging by R-value â is vital to determining a log homeâs energy efficiency.
Moisture Content
The moisture content of timbers used in log home construction is crucial to predicting the amount of settling that will occur in your home. Moisture content is expressed as a percentage of the weight of water relative to the dried weight of the wood. Wood may contain âfree water,â between wood cells, and âbound water,â found within the cell walls. Just as human bodies are approximately 60 percent liquid, living trees typically contain more moisture than wood.
The moment a tree is cut, water begins to evaporate from the wood as it seeks equilibrium with the relative humidity of its surroundings. Wood doesnât begin to shrink until all the free water has evaporated. The point at which no free water remains and shrinkage begins is known as the âfiber saturation point.â Determining moisture content lets producers predict how much log shrinkage they must accommodate. The lower the moisture content, the more stable the wood.
See also 3 Ways to Conserve Water and Lower Your Bill
Green wood has 30 percent or greater moisture content. This is the condition of newly harvested, healthy trees. The wood fibers are totally saturated with water.
Surface-dry wood has 25 percent or less moisture content. This is the condition of wood two to four weeks after cutting and debarking. The outer 1/8-inch of the surface feels dry to the touch. Many wall logs are sold in this condition.
Air-dried wood has 19 percent or less moisture content. It normally takes at least a year to air-dry wood to this level.
Kiln-dried wood has 15 percent or less moisture content. Logs used in homes require two to three weeks in a kiln to reach this benchmark. If the center of a log is reduced to this level, very little additional shrinkage will occur.
Shrinkage
As wood approaches its moisture equilibrium, it changes dimensionally. Shrinkage is a by-product that can affect log home construction. Why? Wood shrinks unevenly. Most shrinkage occurs tangentially, (i.e., in the direction of the growth rings). Tangential shrinkage causes logs to check, or crack, and the combination of tangential and radial shrinkage can cause an 8-foot-high log wall to shrink as much as 1 to 2 inches when green wood is used.
Most shrinkage will occur between 25 percent and 15 percent moisture-content levels. Even kiln-dried logs, which have had most of their moisture removed, and thus already shrunk, still will shrink slightly.
Log home producers, designers and builders take wood shrinkage into account. (Itâs particularly vital to handcrafters who often work with large-diameter logs that take a considerable amount of time to air dry.) They can calculate the amount of shrinkage logs will undergo and use construction techniques that adjust for it. If your home is properly built according to professionally designed plans, shrinkage shouldnât pose a problem.
See also How to Choose the Right Log Home Builder
Drying Methods
Air-dried logs are stored in a log producerâs yard or under cover for anywhere from six months to two years, depending on the local climate conditions and the log species and diameter. Air-drying is common among handcrafters using large-diameter logs.
Kiln-dried logs are placed in super-sized ovens for several weeks. The heat sweats the moisture out of the logs, and fans evaporate it. This process has the side benefit of killing any insects that may be living in the logs.
Standing-dead timber is another option. Donât be put off by the term âdead.â Its name means that the trees were killed by insects, disease or fire, but left standing in the forest long after whatever killed them has passed. When harvested, logs from standing-dead trees are very dry and stable, making them an environmentally friendly resource and a strong option for log home construction.
Some companies use green logs, which are newly harvested and whose fibers are totally saturated, claiming that there are benefits and cost savings to be had with this option. However, as you conduct your research, youâll find that most manufacturers prefer dried timbers.